|
Key Features
wear testing with multi-pass scratch technique
scheduling software for maximum
productivity - programming multiple scratches on multiple samples
accurate repositioning
technique
film thickness and surface roughness
friction and topography
thin film adhesion failure
|
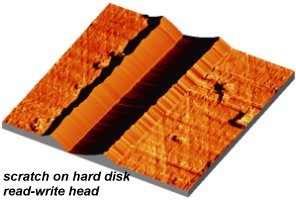
|
Applications
|
Scratch
Testing
In the NanoTest Scanning Module, the sample surface is moved perpendicular
to the diamond probe axis allowing the abrasive wear resistance of a coating
to be investigated by either single or repetitive scratch tests. Accurate
repositioning combined with optional software enables complex multi-pass
scratch tests to be scheduled (with much greater precision than a
conventional scratch tester).
The NanoTest pendulum design is
superior for scratch testing since deformation of the pivot is negligible,
even with very high forces, giving accurate probe displacement results.
For example, sequential constant load
scratches over the same wear track, with a low load topography measurement
performed between each scratch, allow acquisition of elastic and plastic
depth and friction data and the subsequent investigation of friction and
adhesion failure mechanisms.
Data is acquired, analysed, displayed
in real time, and stored under the control of a comprehensive software
package. Six parameters can be recorded (load, depth, transverse
displacement, frictional force, acoustic emission and time), to provide
a wealth of information about the surface. Analysis is simplified with
comprehensive, fully automatic software; all that is required of the
operator is to specify the type of analysis required. For flexibility, data
is saved in ASCII format for spreadsheet and graphics export
.
|
"...Wear processes can be investigated with the multi-pass scratch
technique..."
With the NanoTest, the abrasive wear performance of a coating can be
investigated by means of a multi-pass scratch test. This procedure consists
of sequential constant load scratches over the same track, with a low load
topography measurement performed between each scratch. In this way, changes
in depth and friction can be monitored simultaneously.
...clearly, the success of such a procedure depends on the ability to
precisely and automatically relocate the stylus at the same starting point
prior to each step...
|
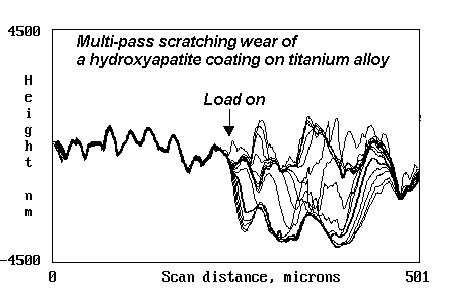 |
Measuring
Coating-Substrate Adhesion Strength by Scratch Testing
The diamond probe is scanned across
the surface under either a constant load or a progressively increasing load
until film failure occurs. Scratching at different locations at constant
load can be used to investigate coating quality and homogeneity.
By ramping the load it is possible to define a critical load (Lc) for
adhesive failure of the coating-substrate system. Film failure can be
detected by several methods using the NanoTest scanning module, e.g., (1) by
the detection of an abrupt change in the displacement of the probe; (2) by a
sudden change in the frictional force between the diamond and the surface;
(3) by microscopic observation of the wear track; or (4) by detection of a
burst of released acoustic energy.
In the example shown below, scratch
testing with the NanoTest Scanning Module reveals clear quantitative
differences in wear-resistance between thin polymeric and inorganic coatings
on the same substrate.
|
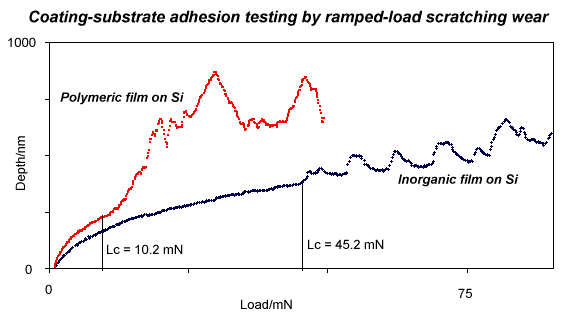 |
|
|