These results were obtained from a weathered automobile
paint system consisting of a steel substrate, primer, metallic paint and
clear laquer overcoat. The penetration depths employed mean that the
results pertain to the overcoat layer specifically.
In the NanoTest, tangential force is
measured by means of a piezoresistive force transducer. This is placed
immediately behind the test probe, which is used to determine topography
variations in the usual way, i.e., by means of the pendulum capacitor, as
illiustrated above.
The plot on the left shows the
simultaneous measurement of the tangential force on a test probe and the
displacement of the probe as it moves over the paint surface at a constant
speed and with a constant applied normal force. The probe was a 3-faceted
pyramidal diamond, the normal force was 50mN, and the scanning speed was
5µm/s.
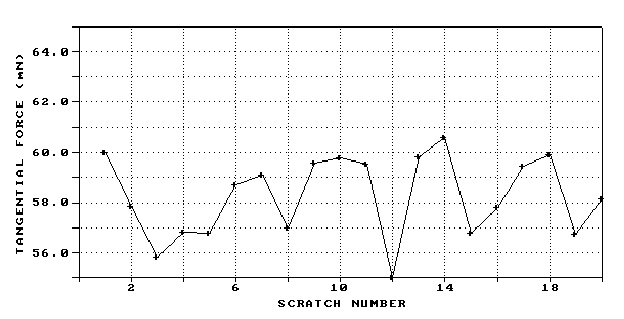
Maximum on-load depth change (below) and
mean frictional force (above) measured for each of 20 scratches. A
25µm
radius spherical diamond was used, the normal load was 200mN, the
scratch length was 1mm, and the scanning speed was 10µm/s.
It can be seen that under
these conditions periodic roughening and smoothing of the surface took
place, i.e., a simple trend towards the production of larger peaks and
valleys did not occur.
A direct
relationship between tangential force and maximum displacement indicating
mechanical interlocking as the mechanism responsible for scratching.
Here, a sharp, pyramidal diamond was used, the normal load was 20mN, and
the scan velocity was 5µm/s over a distance of 500µm